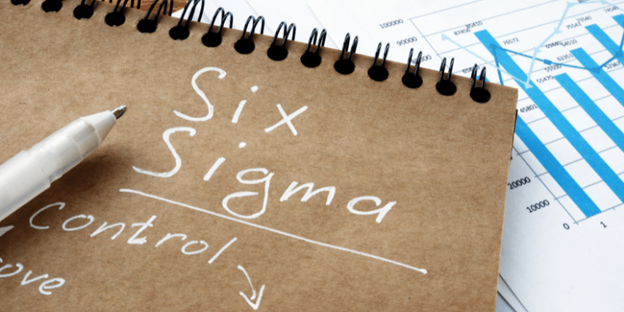
How much does quality and the elimination of waste matter in producing transactional mail? The answer—a lot. Transactional print and mail focuses on mission-critical communications, typically bound by compliance regulations. To live inside such a rigid framework, print and mail providers need to employ numerous methods and procedures. Six Sigma is a quality management methodology focused on improving processes, streamlining quality, and eliminating variances. It is a crucial component to seek out in your provider.
The Link Between Six Sigma and Quality
Six Sigma has several principles which align it with quality and support identifying and eliminating variations in a process. It relies on data to do this, making the method objective. Those practices include:
- Defining the problem, requirements, and goals.
- Measuring the performance of the current process by collecting and analyzing data.
- Analyzing the process to find root causes of variations impeding hitting the goal.
- Improving the process iteratively by removal of those barriers with innovative solutions (e.g., technology and equipment).
- Controlling the new process to ensure it stays on track.
These practices are specific to existing processes, which fit the mold of transactional mail. Our deployment of it to improve transactional print and mail was to adjust and enhance workflows already in place.
By going through each step, quality improves. The change comes from going from an inspection culture to a prevention one. Quality audits are constant and consistent, seeking to understand if there were quality deviations. If found through this data-centric approach, the next action is to improve the process to minimize variations.
Quality cannot be volatile when printing and mailing high-priority personal letters and documents. If quality issues arise, the whole operation is in peril and could be a compliance violation.
How Removing Waste Further Supports Quality
Another principle of Six Sigma is waste removal. It’s process improvement that has a purpose. Waste removal occurs in concert with minimizing variability and creating a continuous flow between tasks. It can include eight types of waste:
- Defects
- Overproduction
- Waiting
- Nonutilized talent
- Transportation
- Inventory
- Motion
- Extra-processing
The sub-groups classify waste in a new way. It’s not just about the foundation of the process; it’s every factor that impacts it, as well. In short, Six Sigma doesn’t let any part of the system slip through the cracks. There’s a concentrated focus at every level of production. Isn’t that the kind of print and mail operation you want to entrust your communications?
Our Six Sigma Certifications and Capabilities
Becoming a Six Sigma organization requires significant work. Quality teams must achieve certification by belts:
- White Belt: Entry-level designation that reports process issues.
- Yellow Belt: Requires a strong understanding of Six Sigma principles and participates in project teams.
- Green Belt: These people start and manage Six Sigma projects and must have detailed knowledge of the methodology.
- Black Belt: This role is mentor, coach, and project leader.
- Master Black Belt: Develops key metrics and strategic direction and trains black and green belts.
At PCI Group, all our Quality team members have a Green Belt or higher. This dedication to Six Sigma enables us to process over three billion images and mail over 450 million packages with a 99.9999% accuracy rate every year.
There’s no room for quality issues or waste in our business. That’s why we employ such quality measures. Learn more about how to sustain quality and accuracy by contacting us today to discuss your transactional mail needs.