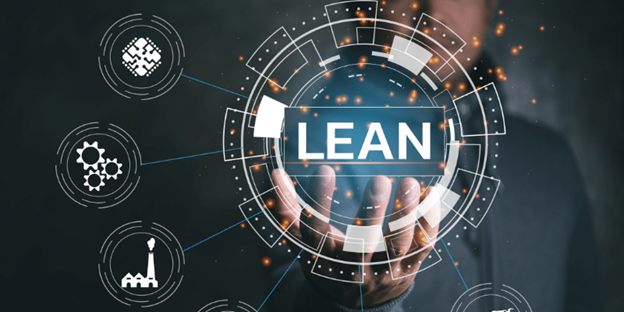
Ensuring the quality of any product requires rigorous processes that are repeatable to maintain consistency and accuracy. That’s especially true for transactional print and mail. So, how do you operationalize this kind of quality? Lean Manufacturing plays a crucial role in the induction of standard works. So, what are they and how do they contribute to quality?
What Are Standard Works?
Standard works describe the establishment of precise procedures and tasks in sequence. In doing so, you optimize this to improve quality and accuracy. These come from 5S and relate to how operators perform the work.
In transactional print, these works include many complicated processes, which may have hundreds of steps. Breaking these down and documenting them enables consistency. Each worker carries out the step in the same way to eliminate deviation and errors.
What Are the Elements of Standard Works?
In Lean Manufacturing, standardizing work includes three components:
- Takt time: The rate of product production needed to meet demand.
- Work sequence: The steps required to perform within Takt time in the order they must occur.
- Standard inventory: The minimum quantity of equipment and materials necessary to run operations.
With these elements at the crux, standard work development can begin.
How Do You Develop Standard Works?
There are many ways to go about developing the steps. In some scenarios, leadership defines them. However, that strategy can be flawed, since management don’t do the work. When we implemented Lean Manufacturing, our approach was to tap our top-performing operators. They do these activities every day, so they are the experts. Having them lead this effort also encouraged greater engagement and buy-in, which is critical in developing a Lean environment.
We now have over 270 standard works! Our staff created them, and employees had to agree that the works were accurate. Within those, the majority relate to actual print and mail tasks. The others are support functions.
How Standard Works Enhance Quality
In deploying these into operations, they have a significant impact on quality. Here’s why.
- Little to no variability: Standardization drives efficiency in processes and reduces variation in output. As such, the work becomes predictable, which can reduce costs while boosting quality and compliance.
- Your people have clear guidelines: When a new operator hits the floor, their training consists of learning standard works. It doesn’t matter who the trainer is or when that new hire comes on board; it’s always the same. Having them actually makes training much easier since there is a single source of truth on how to complete a process. It can also accelerate the onboarding process.
- Continuous improvement is central to maintaining the works: Kaizen, another Lean principle, is the concept of continuous improvement. Standardizing work delivers a foundation for this. To optimize processes, you have to keep improving them. We do that with structured audits regularly to identify any opportunities to do so.
- Scaling the works doesn’t dilute visibility: Transactional printers produce millions of documents weekly. With such a high volume, scaling them is necessary within the same facility and others. these documented processes keep this stable and uniform. Visibility of activities isn’t out of sight when everyone follows the same protocols.
- The focus is on the process, not the person: Workers obviously have to execute the process, but the works put the onus on the process. Process problems can keep efficiency and quality goals unmet. If there are breakdowns or errors where workers are following the them, you know it’s the process that needs retuning.
Standard Works Drive Quality
If quality and accuracy concerns are preventing you from outsourcing transactional print, look for a firm that embodies Lean principles. You can feel confident in allowing experts to handle your critical transactional communications when you know they use standard works.
We’re proud to be Lean, and our adoption of it has led to higher quality and consistency for our customers. Learn more about our dedication to quality!